Pulcino
Pirata
di Jacopo
Faggioni |
|
Storia della costruzione di "Pulcino pirata"
Nascita dell' idea.
Avendo gia' costruito alcune imbarcazioni in compensato marino, desideravo
provare uno scafo a
carena tonda.
Le soluzioni classiche per arrivare a tale risultato erano rappresentate
dalla costruzione in lamellare
e dalla costruzione in "strip-planking"
In ambedue i casi si tratta di metodi costruttivi che permettono risultati
di grande pregio, ma che
richiedono un lavoro di grande precisione e la disponibilita' di uno scalo
indeformabile e,
conseguentemente, di uno spazio dedicato e sufficientemente ampio.
Probabilmente sarei anche stato in grado di impegnarmi in un lavoro di tal
genere, ma ero
spaventato dalla complessita' del lavoro e dalla accuratezza necessaria.
Dovevo, quindi, trovare un metodo costruttivo di maggiore semplicita' e,
soprattutto, di minore
criticita'.
In parole povere volevo poter lavorare in spazi rimediati dove possibile
che potessero essere
cantine, garage, sottoscala o, addirittura, all'aperto.
L'occasione di costruire un diecipiedi nuovo e' arrivata con la richiesta
di mio figlio di poter avere
una barca sua per regatare e per poterci giocare con gli amici.
Le caratteristiche della barca, dunque, dovevano comprendere:
-) facilita' di costruzione
-) buone prestazioni
-) semplicita' di conduzione
-) grande stabilita'
-) solidita' e capacita' antiurto (i genitori pensano sempre che i propri
ragazzi siano degli scapestrati)
-) buona trasportabilita' e facilita' di armamento
Dopo alcune chiacchierate in proposito col figlio arriva una precisissima
commessa dal committente
al cantiere: dovra' essere un catamarano, dovra' essere giallo e dovra'
chiamarsi "Pulcino pirata".
Si va, allora, in cantiere, mi tolgo il cappello di genitore e mi metto il
cappello di cantierista.
Il titolare del cantiere, investito di tanta responsabilita', si mette
immediatamente all'opera
reclutando il migliore progettista di scafi assurdi che ci sia sul
mercato.
Mi tolgo, quindi, il cappello di cantierista e mi metto subito il cappello
di progettista navale.
Cosi' mi ritrovo a dover progettare un catamarano dalla caratteristiche
per lo meno bizzarre.
Per riuscire a rispettare ogni risvolto delle richieste createsi, opto per
un catamarano a carena tonda,
con albero incastrato e non insartiato, con derive fisse, con trampolino
non rigido, con timoni
autosollevabili e senza nessun fissaggio imbullonato.
Pensa e ripensa, alla fine esce un progetto di una semplicita' disarmante.
Si possono vedere i piani sul file "tomcat.pdf"
Ora si trattava di trovare come costruire il tutto senza diventare pazzi.
Ripensando alle mie esperienze di modellista, sono andato a ripescare un
libro di tanti anni fa.
Si tratta de "Il libro completo del modellista navale" di Vic Smeed edito
da Il Castello nel 1976
(preistoria !!!!)
In questo testo viene descritto il metodo costruttivo a sezioni
sovrapposte.
In sostanza si tratta di incollare fra loro vari strati di materiale fino
a creare un oggetto solido.
Questi strati potranno anche essere presagomati in base alle sezioni
derivate dal disegno.
Una volta sovrapposti, si avra' un solido dalla superficie scalinata di
forma grossolanamente simile
a quella definitiva.
Una buona opera di limatura di tutti gli scalini e ci si ritrova con lo
scafo fatto.
|
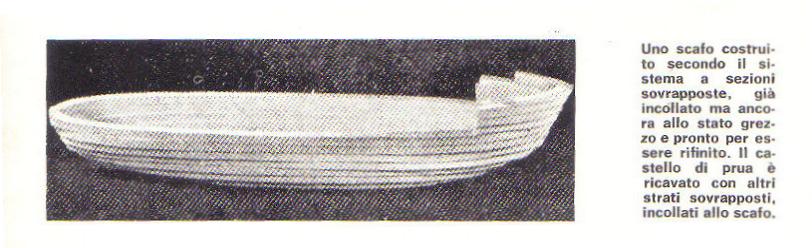 |
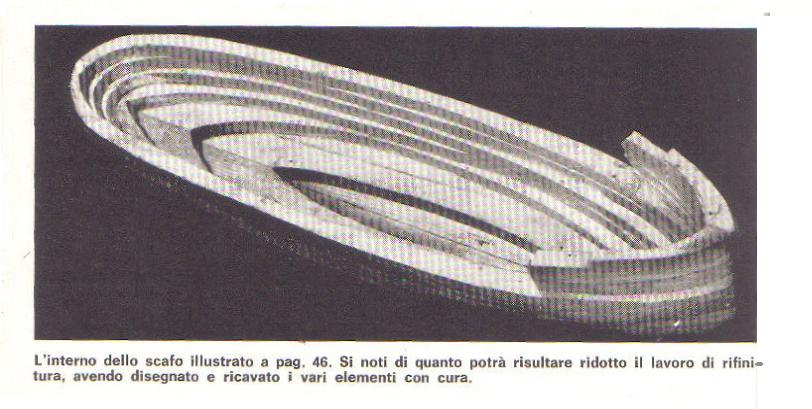 |
Questo metodo puo' essere vantaggiosamente
impiegato con materiali leggeri e disponibili in lastre.
Mi e', cosi', venuto in mente di utilizzare lastre di poliuretano espanso:
quelle normalmente
disponibili per l'isolamento termico dei sottotetti.
Un particolare non trascurabile e' dato dal fatto che e' un materiale
particolarmente economico
Naturalmente si tratta pur sempre di un materiale cedevole e poco adatto a
sopportare sia sforzi
concentrati imposti dalla attrezzatura velica, sia urti localizzati
durante il montaggio, il trasporto o
la navigazione.
Per questa ragione e' necessario rinforzare il materiale espanso con una
stratificazione di
vetroresina.
Normalmente si utilizzano strati di espanso nei quali, oltre alla forma
esterna, siano gia' stati
ricavati anche i vani interni dello scafo.
Di solito, quindi, si procede incollando dapprima i vari strati fra di
loro, uno sull'altro.
Poi si effettua la stratificazione dell'esterno dello scafo.
Infine si esegue la stratificazione dell'interno dello scafo stesso.
All'idea di tutto questo lavoro, dentro e fuori, e per giunta ripetuto per
i due scafi del catamarano,
mi sono sentito un po' demotivato.
Ho pensato, quindi, di tagliare le lastre di espanso solo sul profilo
esterno.
In questo modo avrei ottenuto degli scafi pieni, senza vuoti all'interno e
senza pozzetti o gavoni.
Avrei avuto il vantaggio di dimezzare il lavoro necessario e anche quello
non trascurabile, viste le
premesse, di una solidita' e di una rigidita' strutturale nettamente
maggiori.
Chiaramente avrei ottenuto degli scafi di peso maggiore, ma, in caso
contrario, avrei dovuto
resinare gli interni aggiungendo il peso del vetro e della resina.
Questo peso aggiunto sarebbe stato solo di poco inferiore al materiale
espanso tolto e, quindi, avrei
ottenuto un risparmio di peso meno importante di quanto potrebbe sembrare.
Ringalluzzito da questo “colpo di genio”, mi sono messo all'opera.
Tutti questi ragionamenti, naturalmente, non erano basati puramente sulle
mie fantasie.
Infatti avevo gia' realizzato gli scafi laterali del mio precedente
trimarano con questa tecnologia ed
ero gia' a conoscenza del fatto che il lavoro poteva essere portato a
termine con buoni risultati.
Le immagini riportate qui' di seguito mostrano proprio la costruzione di
uno di questi.
La differenza esistente e' che questi scafetti sono stati costruiti con
lastre tagliate secondo le sezioni
verticali anziche' orizzontali come nel catamarano, ma rimane comunque un
buon esempio per
verificare la validita' del metodo costruttivo.
|
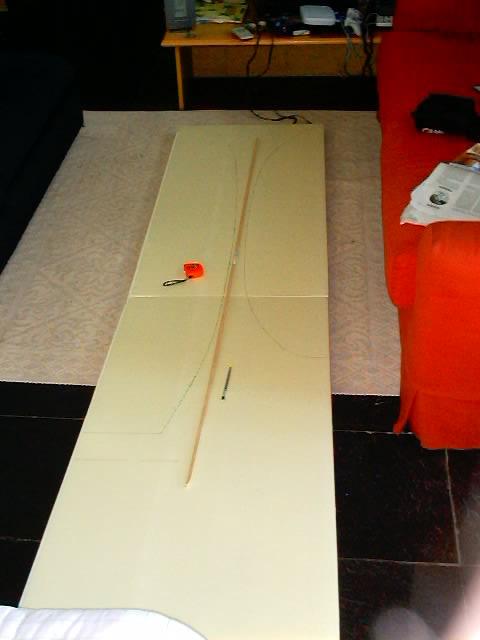
Si tracciano le sezioni sulle lastre di poliuretano
|
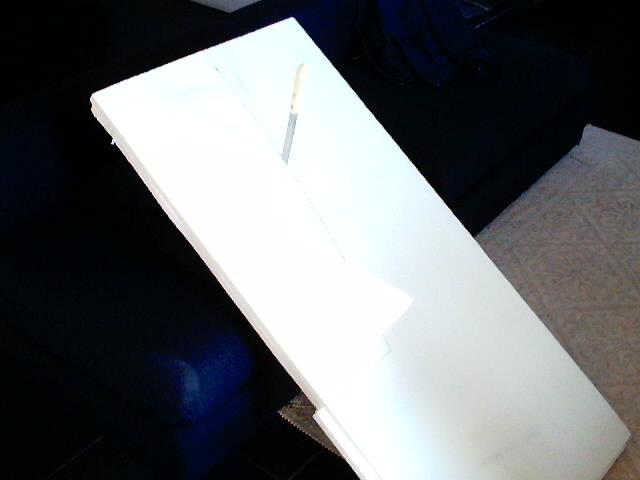 Si tagliano le
lastre. Qui vedete l'operazione effettuata con un utensile professionale:
un coltello
seghettato per il pane.
|
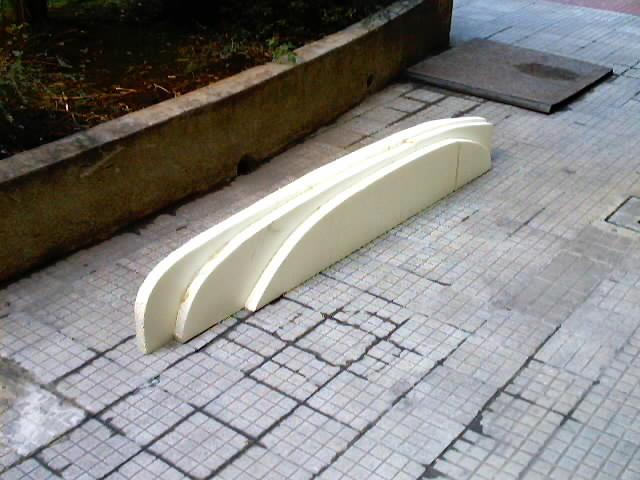
Si incollano le lastre fra loro
|
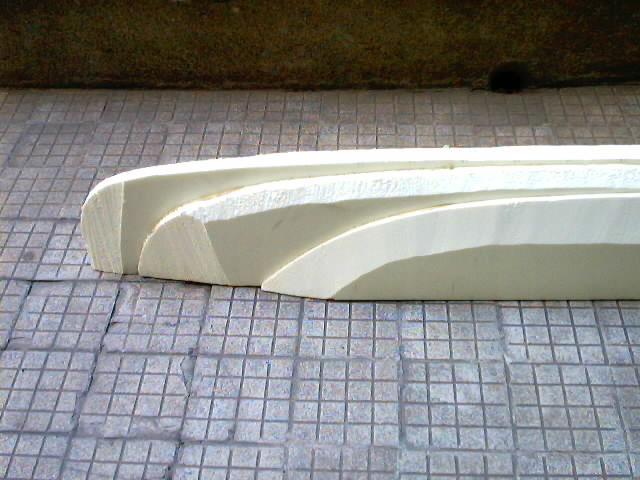
Si da' una prima sagomata a coltello (o seghetto)
|
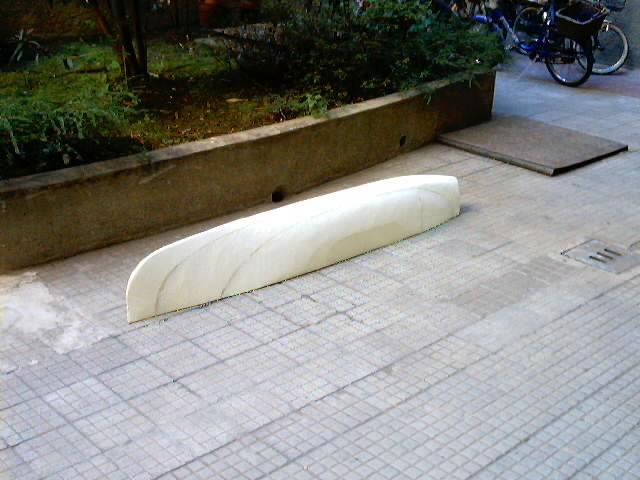
Si sagomano le lastre con lime o carta vetrata
|
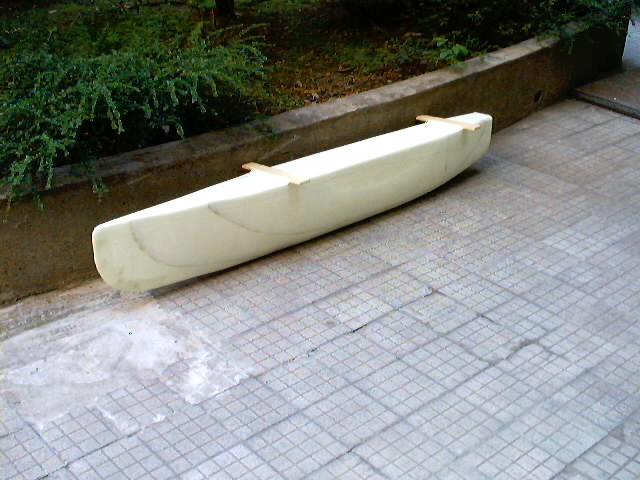 Si incollano gli
accessori e il grosso e' fatto !
Vediamo, ora, che cosa e' successo nel corso della costruzione vera e
propria di "Pulcino pirata"
|
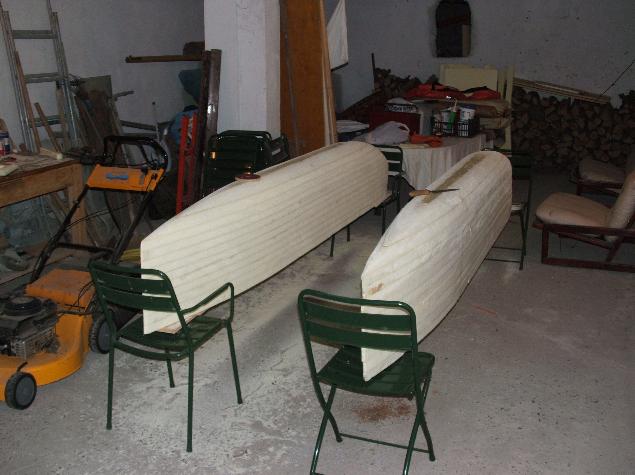 Qui abbiamo gli
scafi gia' riconoscibili.
Precedentemente son state tagliate le lastre, sono state incollate ed e'
stata effettuata una prima
sgrossatura degli scalini a raspa.
|
Lo scafo a destra e' in questo stato, mentre
quello a sinistra ha gia' ricevuto una prima lisciatura a
carta vetrata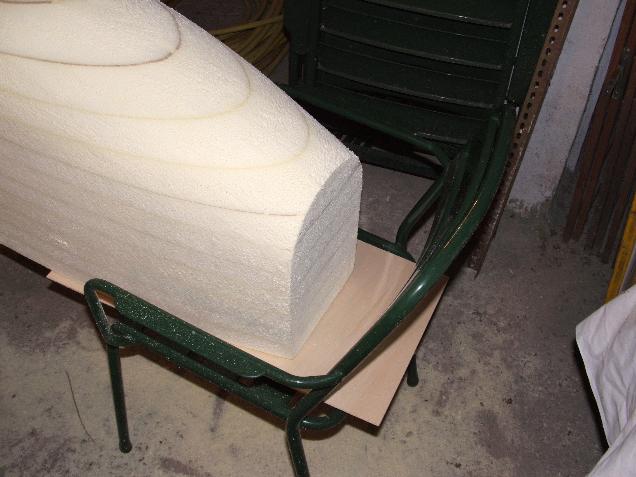
Cosi' si presenta dopo la seconda lisciatura.
|
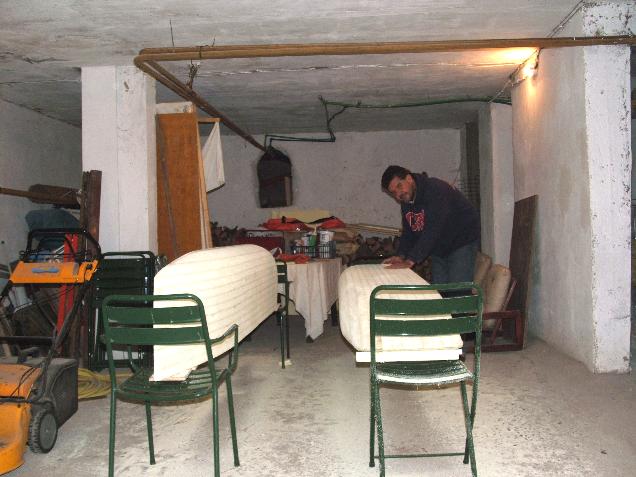
Eccomi impegnato nel lungo e tedioso, ma non faticoso, lavoro di
lisciatura manuale.
|
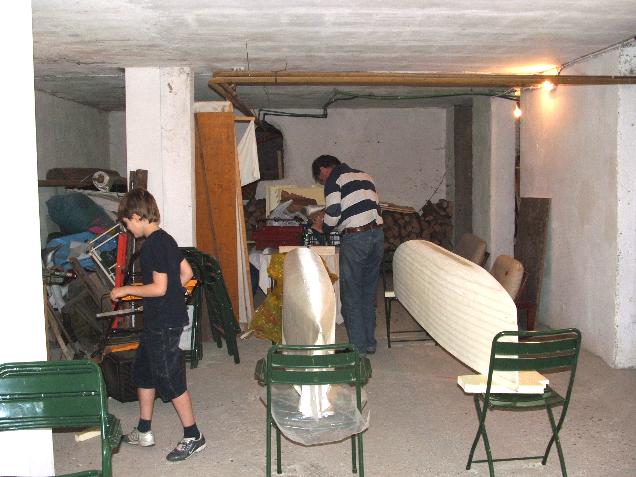
E' stato steso il primo strato di tessuto di vetro e ci si appresta a
versare la resina.
|
 E' stata
completata la resinatura del primo strato, lo scafo e' stato raddrizzato
e si procede a disporre
gli appoggi per le traverse.
|
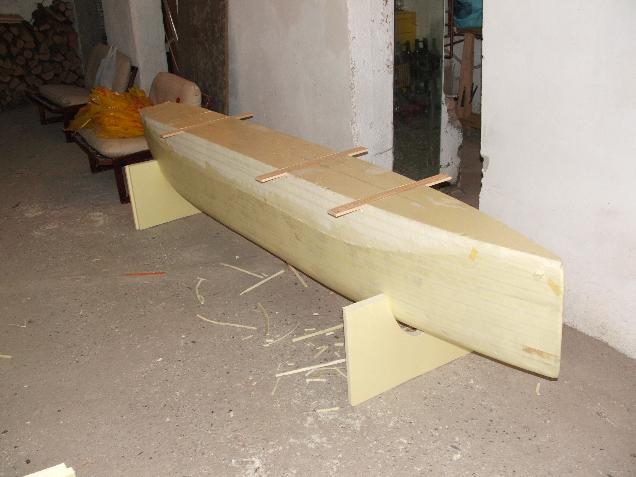
Sono stati incollati gli appoggi delle traverse.
|
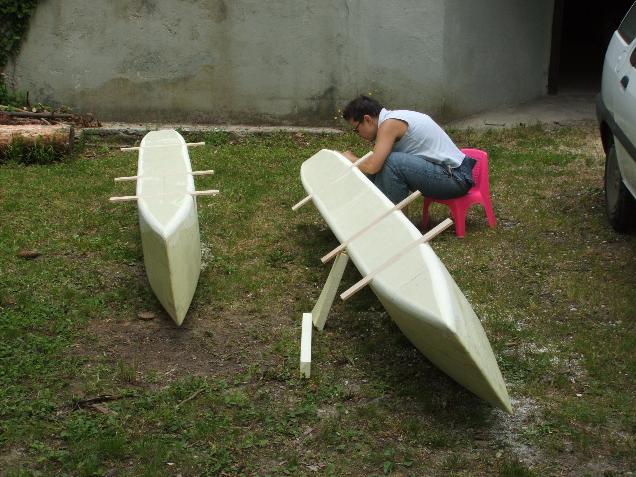
Si provvede alle rifiniture e all'arrotondamento degli spigoli.
|
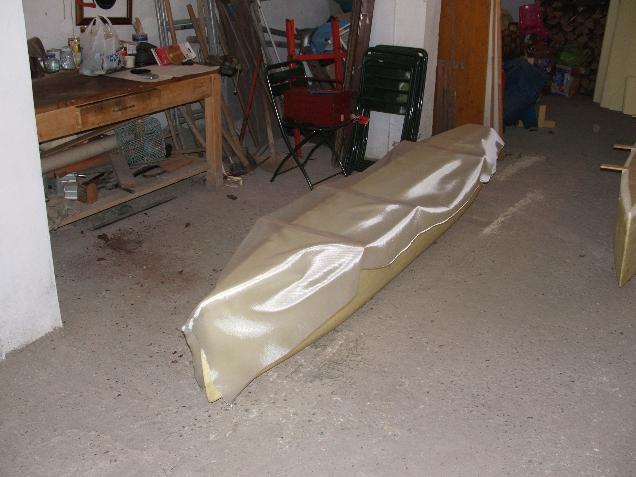
Si stende lo strato di vetro della coperta.
|
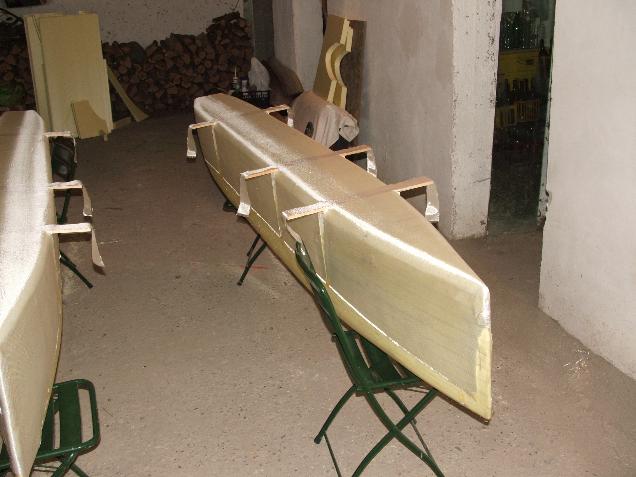
Si ritaglia il tessuto di vetro sulle forme dello scafo.
|
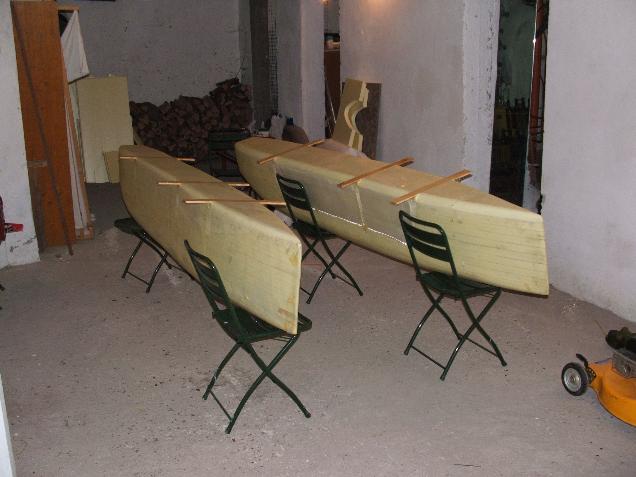
Il tessuto di vetro e' stato resinato
|
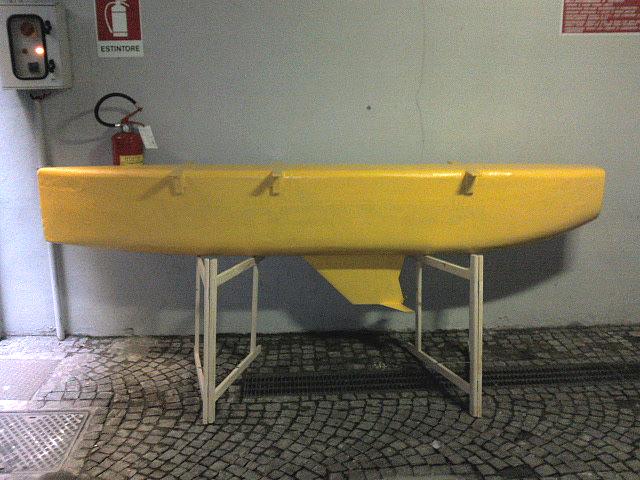 Qui e' stata
inserita la deriva fissa, e' stata completata la resinatura ed e' stata
completata la
verniciatura con smalto lucido all'acqua.
|
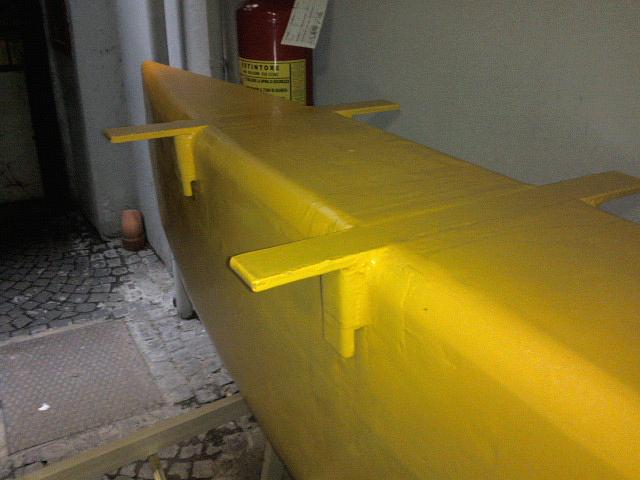
Particolare degli irrobustimenti necessari al fissaggio delle traverse.
|
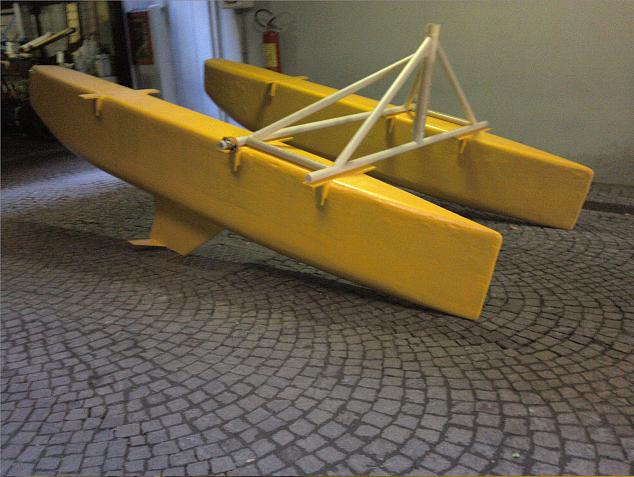 Primo
posizionamento del traliccio di prua che compie le funzioni di doppia
traversa anteriore e di
supporto per l'albero non insartiato.
|
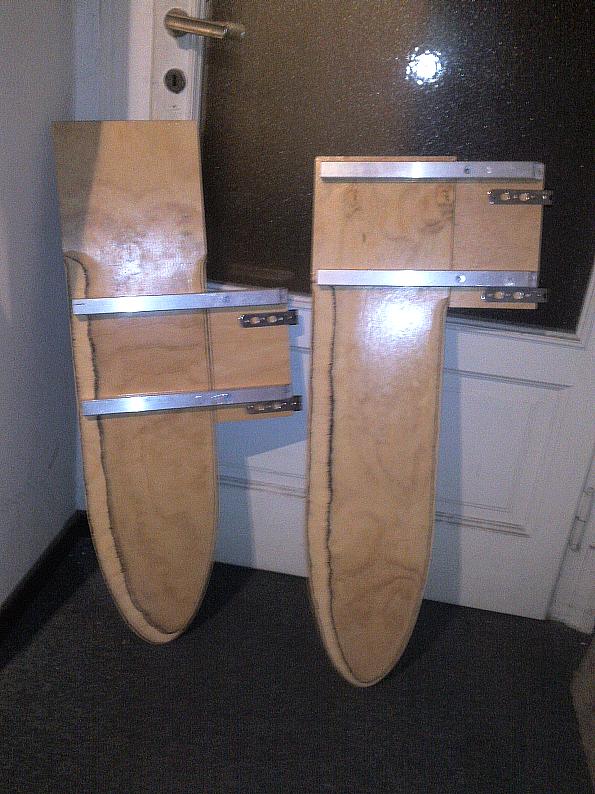 In questa foto
sono mostrati i timoni regolabili in altezza le cui pale saranno
trattenute in posizione
da elastici che ne permettono il sollevamento all'indietro in caso di urto
sul fondo.
|
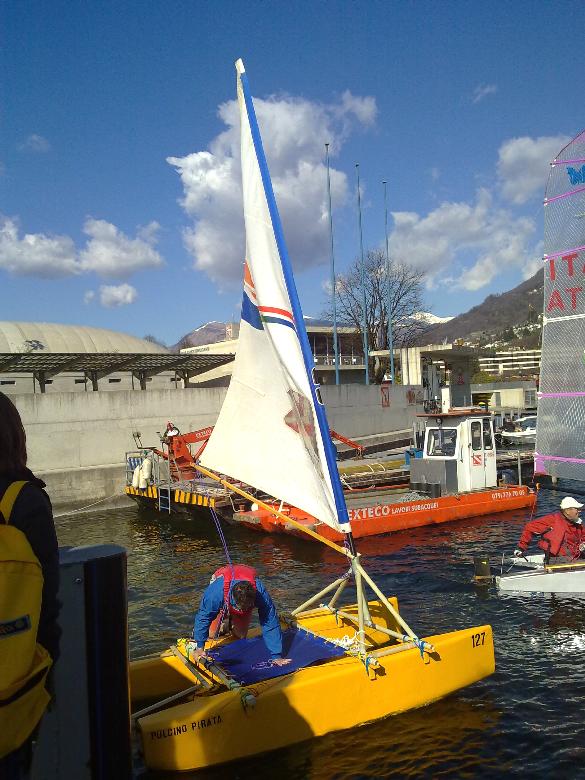
E' il momento del varo e …................
|
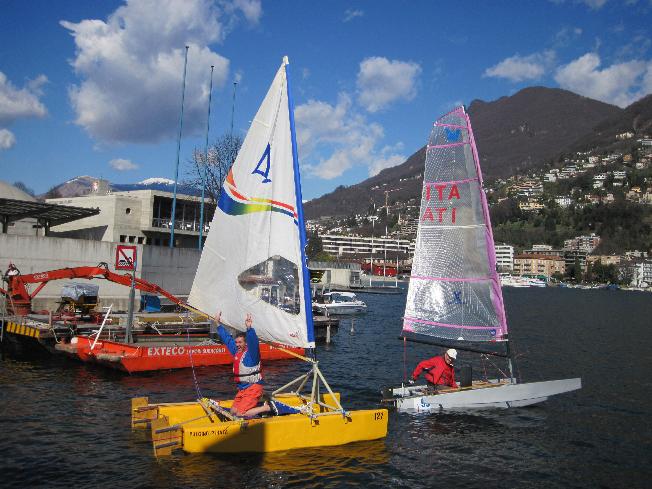
Si' ….. galleggia !!!!!!!!
|
A barca finita,
vediamo di riassumere le impressioni derivate da questo curioso
procedimento di
costruzione.
Si tratta di un lavoro lungo, che diviene tanto piu' lungo quanta maggiore
precisione e cura si
intende mettere nel lavoro.
Questo, a mio avviso, e' il principale inconveniente.
Il secondo lato negativo, rispetto agli altri metodi costruttivi, e'
quello che si ha sempre a che fare
con resine, per lo piu' epossidiche, di cui mi infastidisce il ritrovarmi
sovente impiastricciato mani,
braccia e anche capelli vista la mia proverbiale disattenzione e la mia
incapacita' di eseguire lavori
perfettamente precisi e con la massima cura per la pulizia.
Difficilmente, poi, riesco a non lasciare gocce di resina sul pavimento e
anche su magliette e
pantaloni destinati, cosi', a diventare stracci della polvere.
Mi dicono che basterebbe utilizzare delle leggere tute di materiale non
tessuto per proteggersi !!!!!
Vediamo, ora, alcuni lati positivi.
Il tanto temuto sbriciolamento del materiale espanso si e' rivelato, alla
fin fine, un falso problema.
Infatti il poliuretano forma una segatura grossolana che si deposita
velocemente a terra e che non
possiede quelle fastidiose caratteristiche elettrostatiche tipiche,
invece, del polistirolo.
Nel nostro caso, quando tutta questa segatura si e' adagiata a terra, e'
sufficiente un buon
aspirapolvere per ripulire efficacemente il tutto.
Il maggiore vantaggio e' quello di avere a che fare sempre con elementi di
piccole dimensioni ed
estremamente leggeri.
Il taglio dei pannelli e' un'operazione estremamente rapida ed agevole: un
seghetto a denti fini e'
tutto quanto possa servire.
Il taglio procede molto piu' rapidamente che nel legno: si puo' stimare di
tagliare 5 o 6 millimetri di
pannello ad ogni passata del seghetto.
L'incollaggio dei vari pannelli fra loro si effettua con colle apposite
che non puzzano molto in
quanto contengono pochissimi solventi o, addirittura, con resine.
Per tenere in posizione i pannelli durante l'incollaggio e' sufficiente
appoggiarvi sopra tanti bei libri.
Quando si procede alla carteggiatura, si instaura un rapporto fisico molto
stretto con il nostro scafo.
La mano, mentre passa la carta abrasiva, ha modo di accarezzare le forme e
di individuare ogni
possibile irregolarita'.
Questa fase del lavoro risulta estremamente lunga, come dicevo prima, ma
la si puo' interrompere e
riprendere in qualsiasi momento dato che non esiste alcuna reazione
chimica in atto e si puo'
effettuare a qualsiasi temperatura.
L'aspetto positivo del lavoro e' quello che e' molto poco faticoso.
Si puo', quindi, ascoltare un bel disco e, mentre corre la mano nelle
operazioni di levigatura,
corrono anche i nostri pensieri su infiniti scenari di mari tropicali e
........
Una volta finita la forma, si stende il tessuto di vetro e la resina per
l'impregnazione.
Fatto cio', e' assolutamente necessario levigare la superficie esterna
della vetroresina.
E' un'operazione che puo' anche essere effettuata a mano, ma mi sento di
sconsigliarlo.
La superficie e' piuttosto dura e l'operazione risulterebbe abbastanza
faticosa.
Per fortuna esiste la levigatrice roto-orbitale che permette ottimi
risultati senza fare troppa palestra.
Alla fine la verniciatura e' il lavoro piu' divertente: forse perche' e'
chiaro che siamo ormai alla fine,
ma anche perche' si apprezza il lavoro nella sua forma definitiva e ci si
puo' dedicare alle rifiniture.
Due parole su come naviga Pulcino Pirata ?
Diciamo subito che e' una barca per venti sostenuti: con le ariette,
infatti, soffre un po' il suo peso ed
il fatto di avere sempre due scafi immersi.
Appena il vento monta sopra i sei/otto nodi si scuote dal torpore e
comincia a prendere vita: non ha
problemi di stabilita', stringe una bolina degna di un monoscafo e, al
lasco, arriva a tirare delle
planate da brivido !
Volendo solo andarci a spasso, la sua grande riserva di galleggiamento
permette di navigare
comodamente in due o anche in tre persone ed il trampolino offre spazio
per tutti.
Vi ho fatto venire l'acquolina in bocca ?
Bene, se lo fate anche voi saremo sempre di piu' a divertirci insieme !!!
Vi sono sembrato un po' di parte ?
Che volete fare ! Ogni scarrafone e' bello a mamma sua !
Ciao a tutti !
Jacopo
|
Pdf con questa descrizione
Pdf con misure |
Indietro |
|